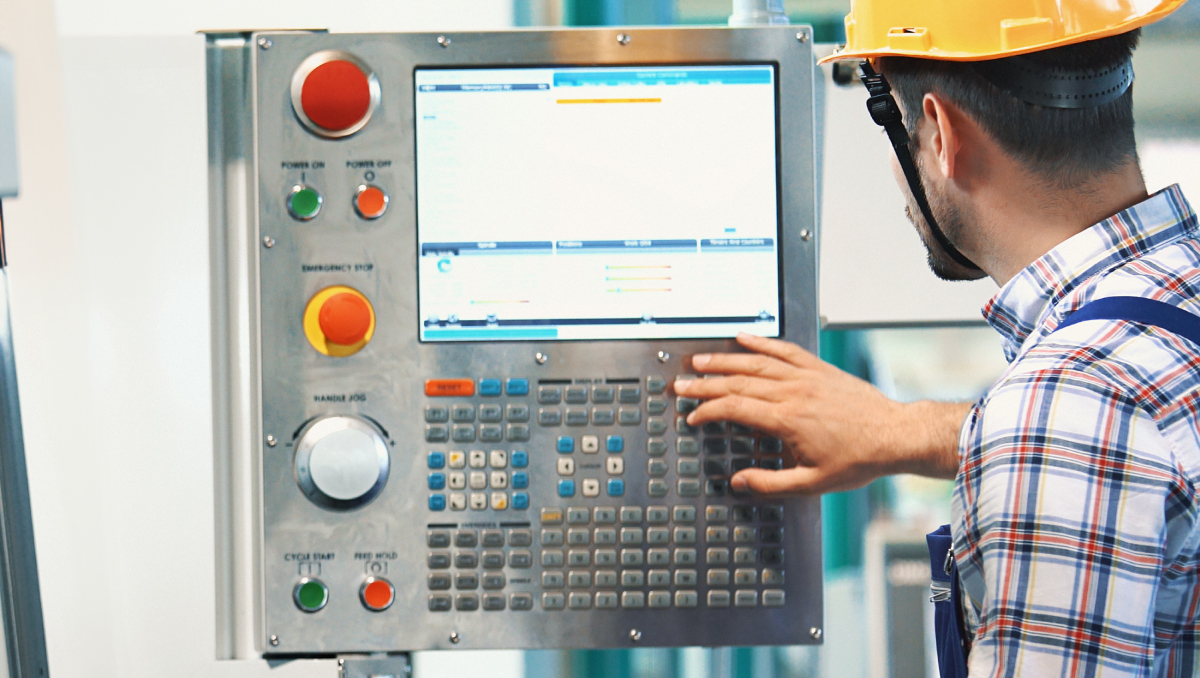
What is HMI: Definition, Trends, and Key Features You Must Know
The human-machine interface (HMI) is the primary information transfer and exchange bridge between the operator and the machine or system. It is also a key ingredient for industrial automation. The HMI is typically touch-capable, with a visual UI that makes it easier for operators or maintenance personnel to operate and monitor equipment directly. The HMI shows a lot of information on the screen, such as temperature and pressure readings, manufacturing process steps, and material measurement data. It can even display the exact location of materials in the equipment or the precise fluid levels in the storage tank. HMIs are central to precision control and monitoring in manufacturing, energy management, and other vital automation industries.
According to a research report by Spherical Insights & Consulting, the global HMI market size was 5.83 billion USD in 2022 and is expected to climb to 17.46 billion USD by 2032. This rapid expansion is attributed to the following factors:
- The drive for innovative technologies:
With continuous advancements in technologies like touchscreen displays and voice recognition, HMI solutions have significantly improved in efficiency and ease of use. - Increasing demand for industrial automation:
The global manufacturing industry’s growing need for automation and data consolidation continues to rise, directly driving the demand for efficient HMI solutions. - The development of smart manufacturing and industrial IoT (IIoT):
The rise of smart manufacturing and IIoT offers broad application prospects for advanced HMI systems, especially in providing in-depth data analysis and enhanced system control.
Two Major Advantages of HMI in the Automation Field
HMIs are indispensable in industrial automation because of their two main advantages: intuitive operation and data visualization. The intuitive operation comes from HMIs providing an interactive platform, allowing operators to control automation systems effectively. This interface enables real-time monitoring of the production process, quick machine setting adjustments, and agile responses to anomalies. For example, in the machining industry, operators can quickly adjust the cutting parameters of CNC machines through the HMI to meet different material or design requirements.
As for data visualization, HMIs enable operators to make quick decisions in real-time by monitoring and visualizing essential data from the production process, thereby improving operational efficiency and system reliability. This capability is particularly significant in real-time tracking on production lines, such as monitoring product assembly speed and quality inspection results, helping operators promptly detect and resolve equipment failures or quality issues, and ensuring efficient and continuous production.
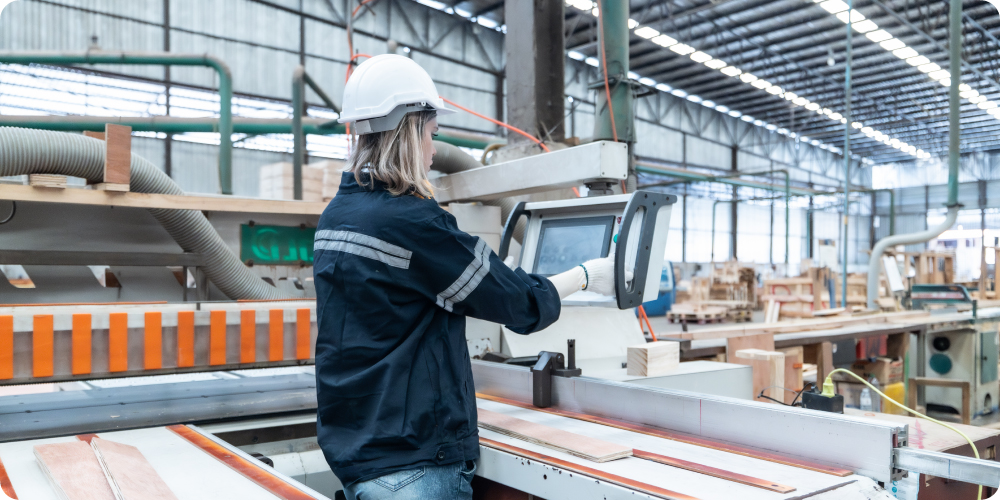
Rugged Features Required for HMIs
In industrial automation, equipment with an HMI is often exposed to harsh and challenging environments. To meet these challenges and ensure long-term reliability and performance, the HMI must have the following rugged features to ensure durability.
- Shock resistance
HMIs are often installed in environments with constant vibration, such as on manufacturing floors or mobile equipment, so they must withstand continuous vibration and occasional shocks to ensure uninterrupted operation. - Wide temperature range
The temperature conditions of the installation environment are also a challenge. From the low temperatures of frozen food processing plants to the high temperatures of steel mills, the operating temperature range for HMIs should be -20℃ to 70℃ to ensure optimal performance and durability under these harsh conditions. - Ingress protection
Frequent equipment cleaning is part of the daily routine in places such as food processing plants. HMIs need at least an IP65 rating for dust protection and waterproofing to withstand regular wiping or direct water washing, effectively preventing water ingress and potential equipment damage. - Fanless design
In sawmills and forging plants, large amounts of sawdust, iron filings, and other particulates can enter through the fan openings, clogging up the panel PC internals. A fanless HMI prevents these particles from accumulating inside the device, increasing the performance and lifespan. - Power protection
HMIs should have a wide voltage range (9–48VDC), as well as overvoltage, overcurrent, and ESD protection, to ensure stability and reliability in various industrial environments.
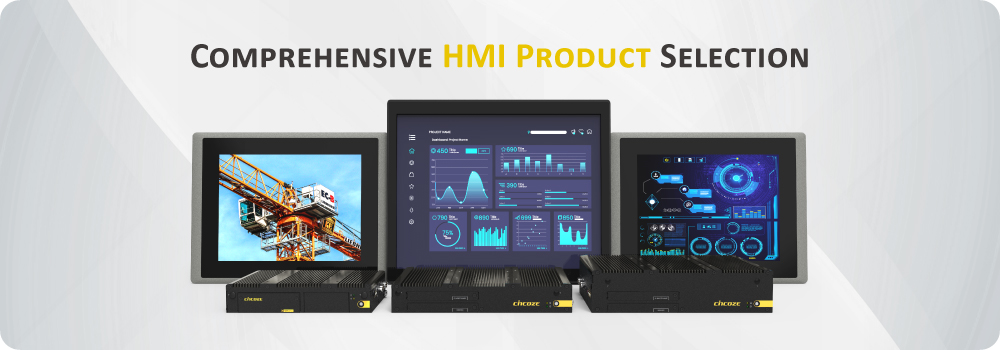
Comprehensive HMI Product Selection
Cincoze offers three comprehensive and complete HMI product series catering to various needs, from industrial panel PCs required for harsh industrial environments to sunlight readable panel PCs for outdoor high-brightness applications and open frame panel PCs that integrate seamlessly with machine equipment. Customers can choose the most suitable panel PC for their HMI application based on the use environment and requirements.
In addition to the performance options of Intel Core and Intel Atom processors, the rugged features are a strength of the Cincoze HMI product lineup. The entire range includes industrial protections, such as an IP65 rated dustproof and waterproof front panel, wide temperature design (-20℃ to 70℃), overvoltage protection, overcurrent protection, ESD protection, and more. U.S. UL safety certification ensures maximum safety, verifying protections against safety issues such as contact leakage and flammable materials and ensuring reliable operation in industrial environments.
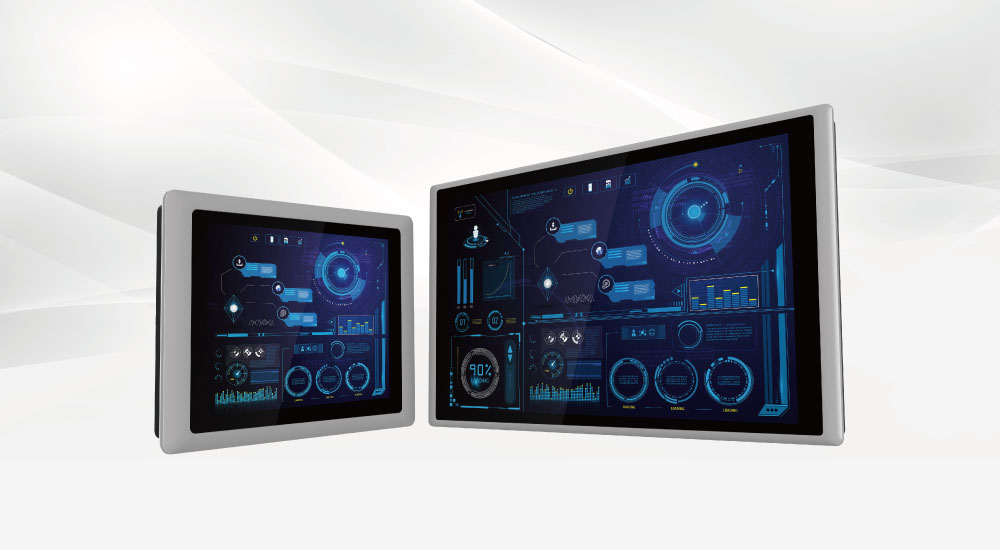
Industrial Panel PC
(CV+P Series)
With the broadest applicability, this series provides various options for screen size (8.4”-24”), display ratio (4:3, 4:5, 16:9), and touch methods (multi-point capacitive and single-point resistive). It is recommended for smart manufacturing and indoor HMI applications.
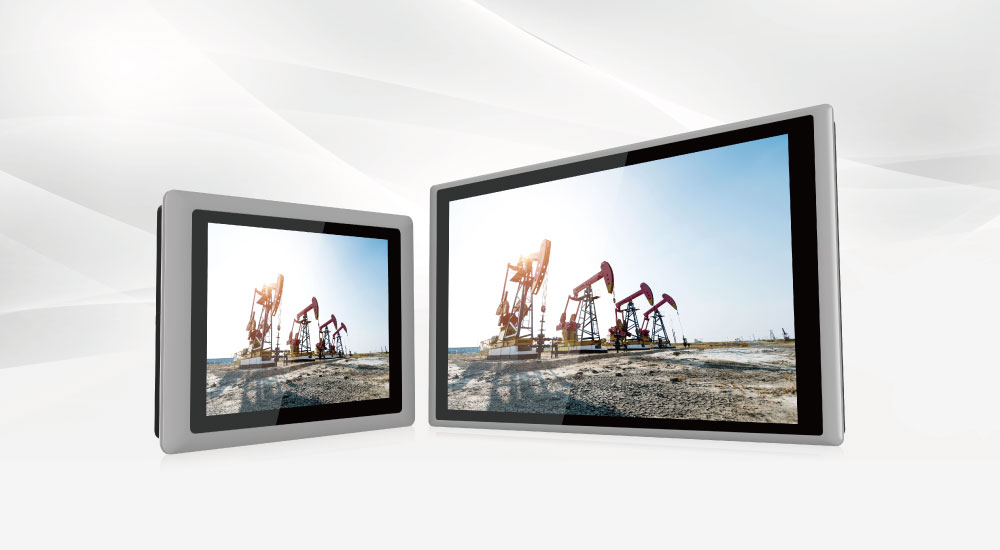
Sunlight Readable Panel PC
(CS+P Series)
With a brightness of up to 1,800 nits and FHD resolution, this series also offers multi-point P-CAP touchscreen functionality and screen sizes from 8.4”-24”, making it suitable for HMI use in outdoor energy extraction equipment and outdoor charging piles.
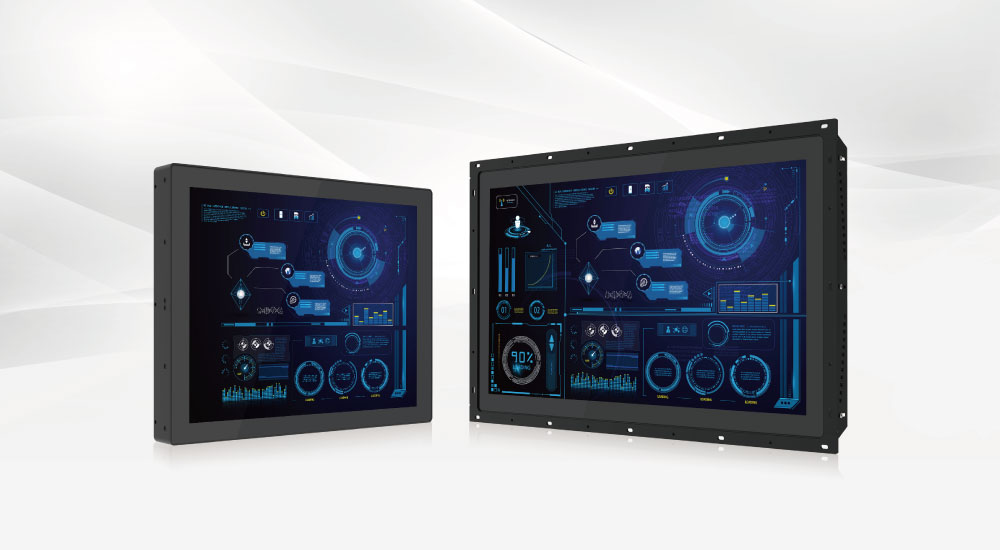
Open Frame Panel PC
(CO+P Series)
Breaking the stereotypes of open frame panel PCs, the patented adjustable mounting bracket greatly simplifies tedious on-site installation. No matter whether using a flat or standard mount, it can fit perfectly in the cabinet. It is the first choice for advanced equipment machine manufacturers. (Patent No.: D224544, D224545, I802427)