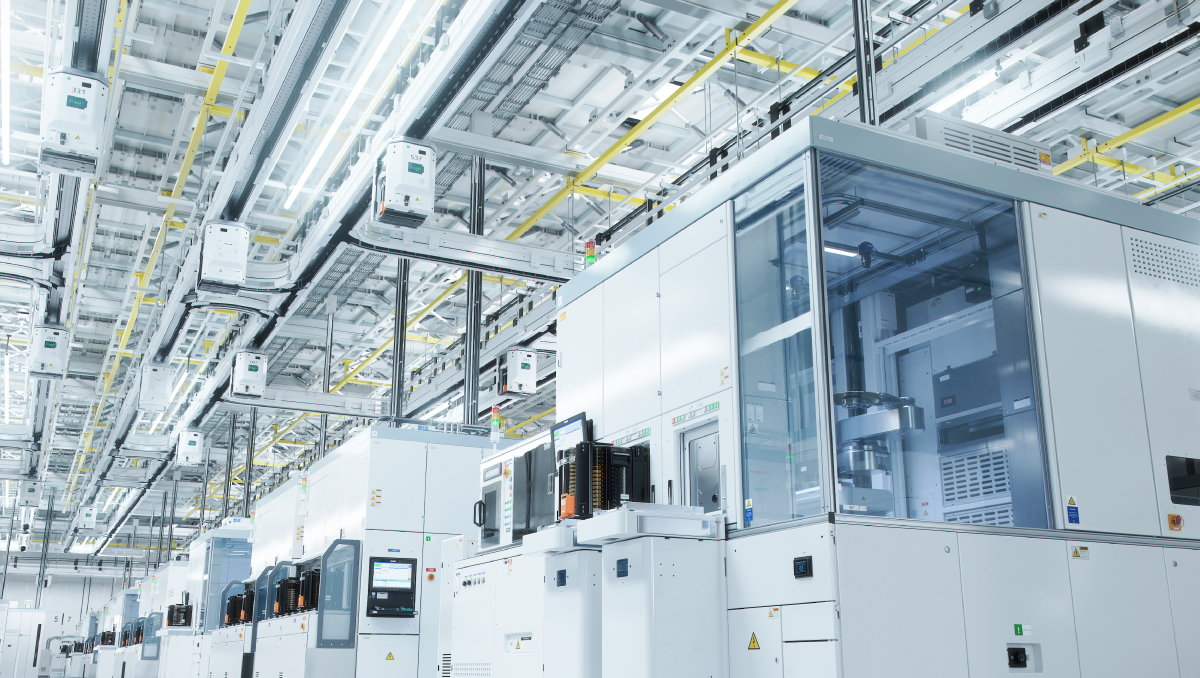
Predict to Prevent: Predictive Maintenance Reduces the Risk of Operational Downtime
Predictive maintenance, powered by sensors, IoT, and AI, allows for continuous real-time equipment monitoring and data analysis, enabling repairs or maintenance at the optimal time, before issues arise. Predictive maintenance presents a major leap for smart manufacturing, creating a shift away from the preventative and reactive maintenance paradigms to a more cost-effective approach that reduces expensive equipment damage and costly early repairs.
Unlike traditional maintenance that responds passively to breakdowns or follows a fixed schedule, predictive maintenance takes a proactive approach by basing maintenance needs on the actual condition of the equipment. This approach not only reduces the risks of unexpected downtime and lowers maintenance costs, but also extends the equipment's lifespan, enhances production efficiency, and enables more flexible and cost-effective enterprise maintenance planning. Predictive maintenance is quickly becoming a key strategy for businesses looking to increase competitiveness and undergo digital transformation.
Three must-haves for predictive maintenance
Predictive maintenance implementation requires integrating technology on multiple levels to create an effective and intelligent maintenance system. This process entails collecting and monitoring data from equipment, combining edge computing and IIoT(Industrial Internet of Things) for real-time processing and preliminary data judgment, and then transmitting the data to the cloud, where AI and machine learning can perform in-depth analysis and make maintenance predictions.
Real-time data collection and monitoring
Real-time equipment status monitoring hinges on continuous data collection from vibration, temperature, current, and pressure sensors. This data is the basis of predictive maintenance judgment and lays the foundation for subsequent training and optimization of cloud AI prediction models.
Edge computing and IIoT
Real-time preliminary analysis and data judgment, performed by data-collecting edge computing devices in close proximity to the equipment, enhances data processing efficiency and minimizes latency. Through IIoT, devices can communicate rapidly with edge nodes and transmit pertinent data to the central system or cloud platform. This stage improves response times and reduces the strain on cloud resources, enhancing overall stability and response time.
AI and machine learning
AI and machine learning are where the magic happens. After front-end data collection and edge processing, key data is sent to the cloud platform for in-depth analysis by AI and machine learning models. These models use real-time and historical data to ascertain the current operation of the equipment and perform anomaly detection, fault prediction, and life assessment. Continuous algorithm optimization helps predictive maintenance foresee potential problems and provide recommendations on the best maintenance opportunities, helping companies reduce maintenance costs and improve equipment reliability.
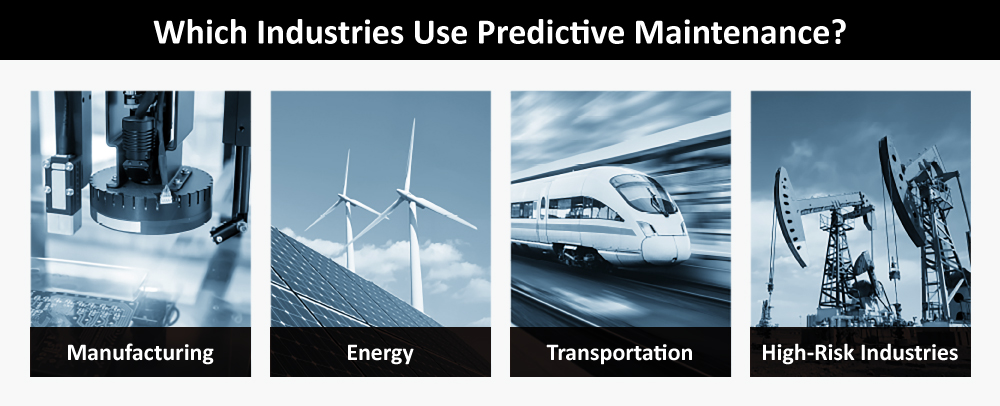
Which industries use predictive maintenance?
Predictive maintenance is best suited for high-risk, high-cost, and high-continuity industries that require stable equipment operation and reduced unplanned downtime.
Manufacturing
Factory equipment often runs 24/7, and this continuous operation leads to parts wear and abnormalities. Predictive maintenance improves production efficiency and reduces maintenance costs by monitoring equipment status and predicting the remaining life of parts, so factories can replace them before they cause damage. This proactive approach avoids sudden shutdowns, improves production line stability and productivity, and optimizes maintenance schedules for times with the least impact on production, such as during planned shutdowns. Additionally, predictive maintenance reduces overall maintenance costs by eliminating unnecessary scheduled maintenance and enabling more accurate parts purchasing.
Energy
Predictive maintenance reduces the hassle and expense of equipment maintenance in remote locations, such as solar and wind power plants. AI predictive maintenance monitors the operational data of key components, including gearbox oil temperature and turbine blade vibrations of wind turbines, as well as voltage and solar converters at solar farms. Combined with environmental data analysis, it is possible to improve energy production stability and overall operational efficiency by accurately predicting potential failures and significantly reducing unplanned maintenance.
Transportation
Predictive maintenance offers significant benefits to the rail transit and aviation industries, where equipment reliability is paramount but maintenance and overhaul costs are high. By instantly analyzing the status of critical components like train wheels and bearings, or aircraft engines and landing gear, and integrating this data with maintenance records and environmental information, predictive maintenance can detect abnormalities before they result in equipment failure. This not only ensures the safety of rail and air travel but also optimizes maintenance schedules and minimizes disruptions to transportation services caused by unplanned outages.
High-risk industries
Equipment failure in refineries and chemical plants can lead to production interruptions and safety accidents, resulting in substantial economic losses. AI and sensing technology enable companies to monitor equipment conditions such as pressure, temperature, vibration, corrosion, and leakage, and identify potential abnormalities early on. This proactive approach prevents equipment overload, ensuring production safety and stability.
Cincoze industrial computers: The cornerstone of predictive maintenance
Predictive maintenance hinges on edge computing and IIoT, powered by stable, high-performance industrial computers that can cope with harsh environmental challenges. These industrial computers ensure real-time processing and accurate judgment to support the reliability and immediacy of the maintenance system. Cincoze industrial computers are the ideal choice due to their rugged design, flexible expandability, and diverse performance options.
Rugged design for harsh environments
Cincoze industrial computers are designed for harsh industrial environments, with wide temperature (-40°C - 70°C) and wide voltage (9 - 48 VDC) support, vibration resistance, and fanless design. These features ensure that the Cincoze industrial computer, as the core of the predictive maintenance system, can maintain stable and reliable performance under high loads and long-term operation. They are ideal for various severe application scenarios in manufacturing, energy, transportation, and high-risk industries.
Flexible expansion for diverse data collection
The in-depth analysis needed for predictive maintenance requires multi-dimensional data collected from field-side connections to many sensors, such as vibration, sound, temperature, voltage, and weight sensors. Many field-side data collection computers have a fixed selection of I/O ports that limits them to very specific use-cases. Cincoze industrial computers have a modular expansion design, allowing users to flexibly expand the required I/O interfaces based on what the application needs, and enabling enterprises to integrate more sensors or devices and expand their predictive maintenance systems without replacing their hardware. This saves time and money because the module can be swapped to accommodate new data collection requirements.
Wide range of performance options for specific applications
Cincoze provides industrial computers with multiple performance levels from basic data processing to high-performance edge AI computing. Whether the predictive maintenance system requires powerful computing power to perform complex AI analysis and fault prediction, or only requires entry performance for daily monitoring, Cincoze provides configuration options that ensure the efficient and stable operation of the predictive maintenance system.