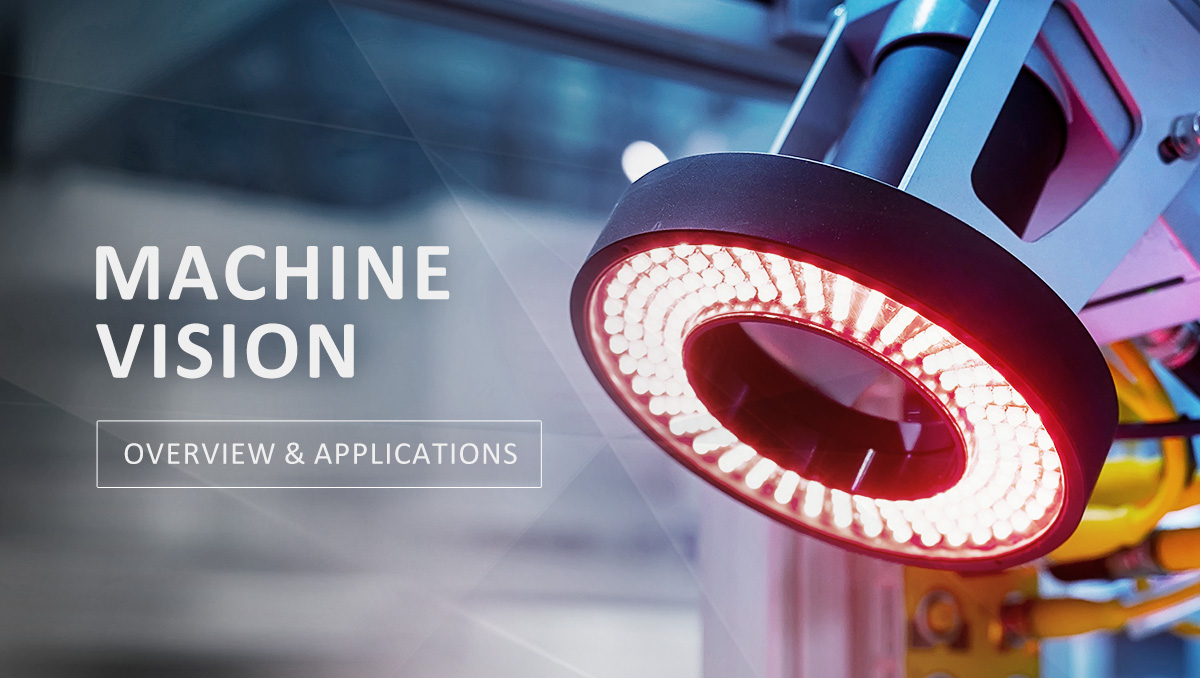
Machine Vision: Overview and Applications
Machine vision is the eyes of Industry 4.0. It is the pivotal technology that empowers manufacturing automation systems to capture visual inputs, make decisions, and take actions completely on their own. The Association for Advancing Automation (A3) defines machine vision as the combination of software and hardware used to analyze and process images or videos to provide guidance and assistance during the execution of industrial equipment. As an alternative to manual labor, machine vision provides faster, non-contact, and higher accuracy automation for guidance, identification, measurement, and inspection.
Since its beginnings in the 1990s, mainly in the semiconductor, electronics, and automotive industries, machine vision has rapidly seen adoption in other fields, such as surveillance, medical, robotics, autonomous vehicles, and drones. These expanded applications have ignited new growth in the global machine vision market and according to Research and Markets, it is expected to reach 25.92 billion US dollars by 2030 with a 7.7% CAGR.
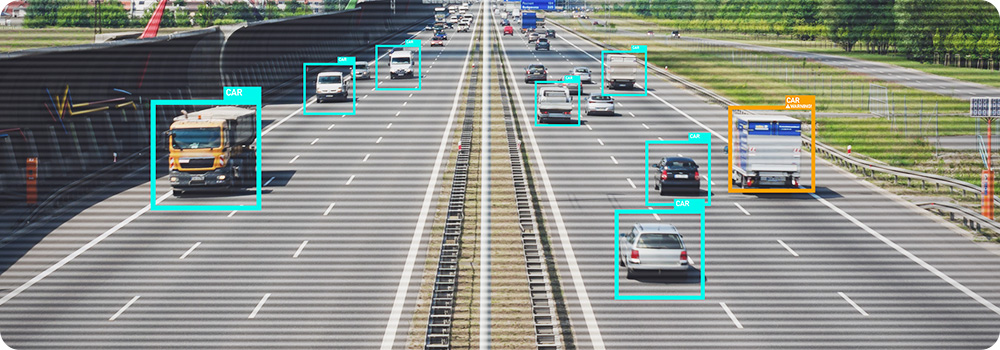
Components of a Machine Vision System
Machine vision describes a system consisting of various components that perform different functions to allow a computer system to “see” the real world. The most commonly found components of a machine vision system are described below.
- Lighting :Machine vision needs images for analysis. The clearer, brighter, and more detailed an image is, the better the machine vision system’s image processing software can analyze those images. Good lighting, typically using flash or LED lights, provides the illumination needed for capturing the best quality images.
- Cameras and Lenses :A well-lit picture is only as good as the camera it is taken on. CCD cameras, CMOS cameras, and special machine vision cameras capture images and send the data through the image capture card to the computer for subsequent processing and analysis.
- Image Capture Card :The image capture card provides a high-speed interface between the camera and the computer, converting the camera output signal into a digital signal. The image capture card determines the maximum possible frames per second at a given resolution.
- Computer :Image processing is done by the computer’s CPU and GPU. For deep learning training and inference, a high-performance CPU and additional GPU power are required for optimal performance.
- Image Processing Software :This software processes images to extract, analyze, and identify features in the image.
- Display :The results obtained after image analysis can be displayed on a monitor, and the next action or mechanism can be triggered through the user interface.
- Control System :COM and DIO signals trigger and control machinery such as PLCs and motors.
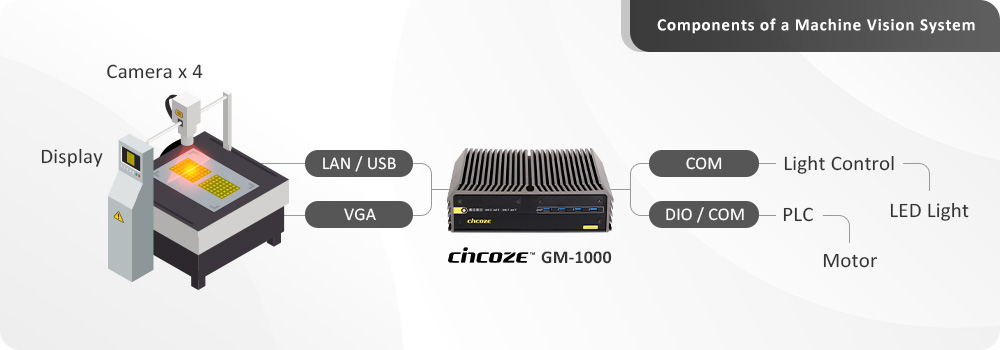
Applications of Machine Vision
Machine vision applications are seemingly endless and new ones are coming out all the time. However, there are four main areas where machine vision has seen the most development and adoption.
- Industrial Automation
- Quality Inspection:Manufacturing was the first industry to use machine vision to optimize its processes, mainly for automated optical inspection (AOI). AOI uses cameras to scan the surface of an object and detect color irregularities or defects.
- Navigation:Autonomous mobile robots (AMRs) and automated guided vehicles (AGVs) use machine vision, radar, and lidar to perform 3D perception and recognition of the working environment so that the robot can navigate autonomously to its target location.
- Security Monitoring
- Face Recognition:Detect and recognize faces from images or videos with the aid of machine vision, then compare them to a database of known faces. This identification in airports and border control speeds up detection and security management.
- License Plate Recognition:Automatic number plate recognition (ANPR) uses optical character recognition (OCR) to recognize the license plate number captured by a camera. In smart transport infrastructure, ANPR brings more efficient and convenient traffic management.
- Anomaly Detection:Uses machine vision image recognition technology to automatically detect hazardous situations in surveillance images, such as intrusion or theft, or natural events like flooding or fire. When an event is detected, the system automatically alerts security personnel so they can respond quickly.
- Medical Imaging and Surgical Assistance
Machine vision brings the automatic detection of lesions to medical imaging, such as CT, MRI, and X-ray. Using deep learning and other technologies for image recognition and feature extraction analysis can help doctors diagnose and treat more quickly and with higher precision. Machine vision also plays an important role in surgical assistance, where surgical robots and intelligent instruments can assist doctors with precision positioning, cutting, and suturing required for minimally invasive surgery. Surgery is more precise, operating times are shorter, and doctors are less fatigued. - Autonomous Driving
Machine vision performs multiple tasks in self-driving cars, such as lane line recognition, obstacle detection, traffic sign detection, pedestrian detection, and vehicle detection. The machine vision system’s high-resolution cameras, radar, lidar, and other sensors capture the data of the surrounding environment in real-time and perform feature extraction and image recognition so that the self-driving car has a clear understanding of the environment. For example, in lane line recognition processing, the system performs straight line or curve fitting processing so the self-driving car can recognize and stay in the correct lane. For obstacle detection, machine vision analyzes images and sensor data to determine the shape, size, and distance of obstacles to help self-driving cars avoid collisions.
The Role of Industrial Computers in Machine Vision
Industrial computers are the most stable and reliable computers for industrial use, and they have the necessary processing power and connectivity for machine vision applications. In the real-time analysis of image data, such as image processing, feature extraction, and recognition and classification operations, high-performance industrial computers can meet the needs of these computationally intensive tasks. In addition, the size and speed of the memory and hard disks in industrial computers can be chosen to cope with the ever-increasing demand for data storage.
In terms of communications and connectivity, industrial computers need a selection of I/O interfaces to connect with the other devices, such as cameras and sensors, within the machine vision system. Wireless communications allow the industrial computer to send the analysis results to the control center to inform decision-making. Industrial computers are very stable, and their rugged label signifies that they can operate predictably in harsh industrial environments. These features make the industrial computer an ideal computing platform for machine vision applications.
Cincoze Industrial Embedded Computers for Machine Vision
The Cincoze GPU Computing – GOLD and Embedded Computing – DIAMOND product lines provide a selection of embedded computers with a variety of performance options and expansion capabilities to suit most machine vision applications. These computers are built for harsh industrial environments and can withstand high shock and vibration, extreme temperatures, and power protection. The computers can be customized with additional I/O and functions by adding CMI/MEC/CFM expansion modules. The computers pass many international certifications and industry-specific certifications to provide customers with the most stable and reliable operation.
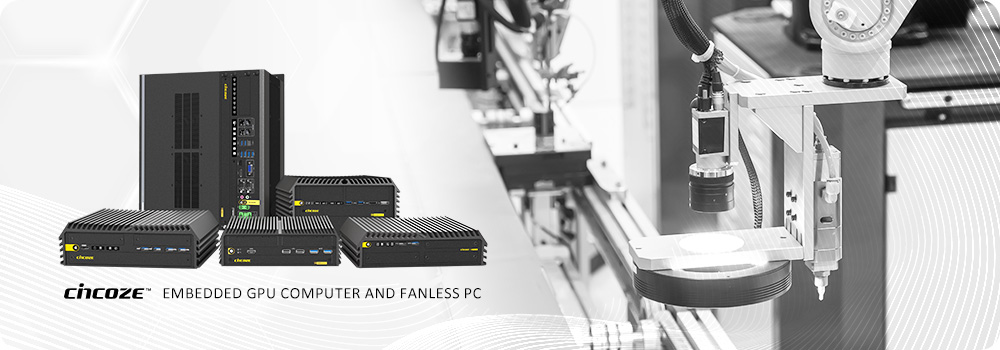
- GOLD Series
- GM-1000:The GM-1000 is a high-performance, compact GPU computer. It supports an Intel® Xeon® workstation-class CPU, is equipped with an embedded MXM 3.1 slot for type A and type B MXM GPU modules, and provides up to 360W of system power. The compact size is ideally suited for robotic arms and other environments with limited space.
- GP-3000:The GP-3000 is a high-performance, scalable GPU computer. It supports an Intel® Xeon® workstation-class CPU, up to two 250W full-length GPU cards, and provides a large total power budget of up to 720W to meet the needs of high-end machine vision. The GP-3000 supports a GPU Expansion Box (GEB), to add more PCIe slots and increase GPU processing capacity. Adding advanced GPUs provides a measurable performance boost that can accelerate complex industrial AI and machine vision tasks.
- DIAMOND Series
DIAMOND embedded computers also provide different form factors, power consumption, and expansion methods, so that customers can choose the most suitable machine vision solution according to their needs. The DX-1200 is equipped with a 12th gen Intel® Core™ (Alder Lake-S) CPU and Intel® Xe UHD 770 graphics chip, and supports 4× 10Gbps high-speed LAN and up to 8× PoE. For applications that require more expandability, the DS-1300 supports an Intel® Xeon® workstation-class CPU and provides up to two sets of PCI/PCIe expansion slots for external frame grabber cards, motion cards, or GPU cards. It also includes the patented “adjustable card retainer” (Patent No. I773359) that locks expansion cards of any size firmly in place. The Intel® Core™ CPU-equipped DI-1100 and DV-1000 are high-performance solutions for mobile devices, such as robots and AGVs. - Use Cases
- Industrial X-ray Inspection System:X-ray inspection is a non-destructive, precise, and efficient quality inspection method for automotive, aerospace, electronics, and other industrial fields. A European X-ray inspection equipment manufacturer chose the highly expandable DS-1302 rugged industrial computer as the core computer in its automatic quality management X-ray inspection system.
- Thermal Imaging System Detection:Smart thermal imaging uses the GM-1000, along with AI and deep learning algorithms, to perform rapid personal temperature monitoring, mask detection, face recognition, and footprint tracking in airports, hospitals, and factories to prevent the spread of COVID-19.
- Automated Track Inspection Vehicle:A railway engineering company installed the GP-3000 on the automatic track inspection vehicle to accurately measure track defects using the machine vision imaging system. They chose to use the GEB to install additional GPU cards, RAID cards, and control cards on the GP-3000, making it a powerful system for image processing and detection in this case.
- Factory AMR:A robot manufacturer used the DS-1202, plus a GPU card, in its AMR to enable automatic picking and unloading through machine vision and robotic arms. The AMR detects the environment dynamically and shuttles through the factory, avoiding obstacles, and transporting items to their destination.
Embedded Computer ∣ Fanless PC ∣ GPU Computer ∣ Rugged Computer ∣ Machine Vision Computer ∣ AOI ∣ Edge AI ∣ Deep Learning